Robotic weld trial at ABB.
- Luke Nixon
- Feb 16, 2018
- 3 min read
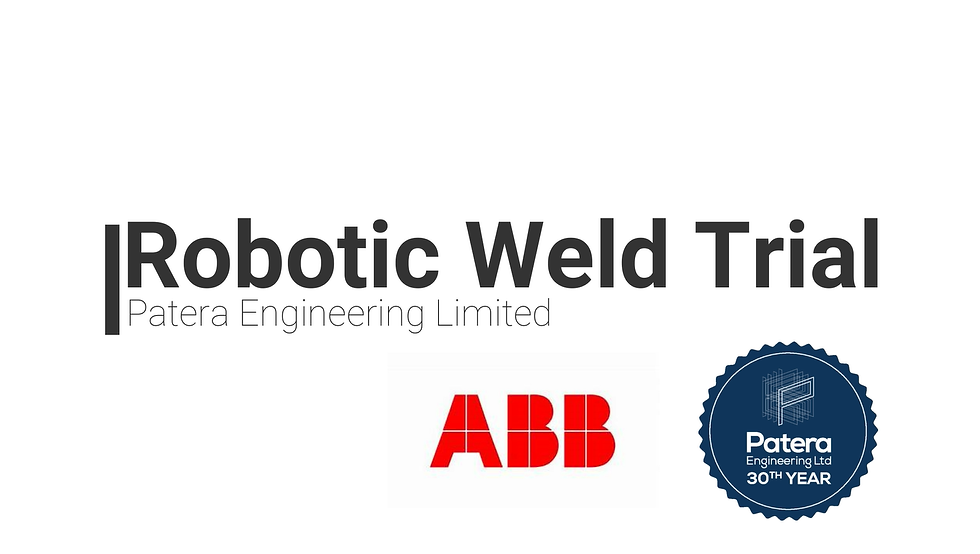
On Monday 12th February, we managed to get a real look at what we can expect with a Robotic weld arm from ABB. Its safe to say we were very very impressed!
Lets take it back a week and run though the process. We decided to to make things simple, we knew the robot could do complicated tasks but how was it doing some of the simpler more monotonous stuff? So we put it to the task of welding some pendant supports for a job we are currently working on with one of our clients.
The first task, we needed to make a fixture. This is the ensure the components can be held in a fixed place for the weld robot to do its stuff. Our Design Draughtsman, Antonio, who has actually had a little experience working with robots in his native country Portugal, was on hand to design it, with a little help from our friends over at ABB too.
Antonio runs us through the different process stages for designing the fixture:
Analysis of the assembly to be welded
Selection of the best position for welding
Initial contact with ABB to discuss the minimum clearance zones for the torch access
Selection on the types of materials, clamps and design concept to adopt
Preliminary 3D model of fixture is designed
3D model is then sent to ABB for a test on Robot Studio and reviewed.
Final adjustments are made according to ABB's recommendations
Construction
Safe to say we had things covered and managed to produce this:
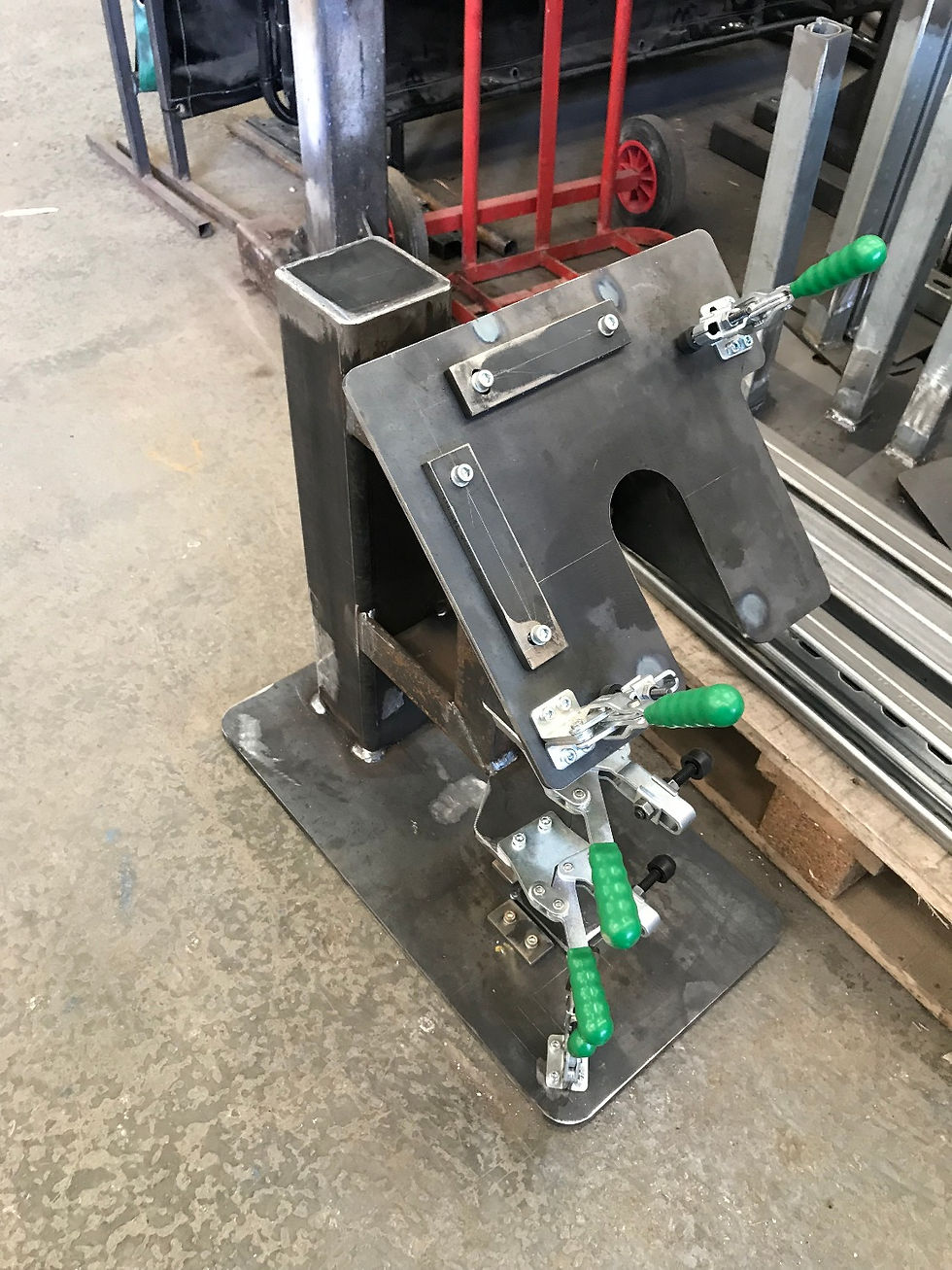
We had some great feedback from ABB, and all credit must go to Antonio for picking this process up so quickly.
We were ready to put it to the test. We transported the fixture and various components down to ABB head office in Milton Keynes ready for us to arrive on the Monday for the big day!
As always ABB were extremely hospitable and we were welcomed with open arms by Business Development Manager, David Green. We got a hot drink from the fancy touch screen vending machine, which needed a soft touch, something us engineers are not too capable of. Luckily David was on hand.
We arrived at the cell where the magic would happen, with our fixture in place and ready to go. We were joined by David Lewis, Innovation Manager from Skanska. We were all very excited to see the robot do its work.
Take a look at this video to see it in action...
Its and impressive piece of equipment, and the final product is great. We were all pleased with the results even though we only had around 2 days of development.
The process of one pendant from start to finish took around 100 seconds. This is with an ABB ooperative loading the fixture, and the robot not running at full speed. It is believed we could shave off another 10 seconds off this process with more practice and further development. It would roughly take one of our workers to put this together in 240 seconds. Of course this is without them having a break and stopping for a chat.
With the robot running at full capacity and with a few adjustments we are going to be producing products like this so easily and quickly. It is an exciting time and we are again one step closer to introducing automation at Patera Engineering Limited!
Watch this space!
Luke
Comments